Deep Hole Drilling System
In Deep hole drilling is the machining of holes with a relatively large depth to diameter ratio. Whereas normal drilling techniques produce holes where the depth is rarely more than five times the diameter. Deep hole drilling in the ratio may reach 150:1, and any hole deeper than ten times the diameter should certainly be considered a deep hole, requiring a specialised drilling technique. Deep hole drilling can employ various machine set-ups: rotating work piece, rotating tool, or both tool and work piece rotating. The most common, however, is for the work piece to rotate, while the tool supplies the linear feed movement. Whichever set-up is employed, the basic principles of drilling still apply, and the correct choice of cutting speeds and feeds are still crucial. Satisfactory chip breaking, and removing the chips from the cutting edges without damaging tool or work piece, is essential.
Is similar to STS, except that the drill is connected to an inner and outer tube. Cutting fluid is pumped down the drill between the two tubes, ie. entirely within the drill body rather than externally, and the chips are flushed back out through the inner one, also within the drill body. This self-contained system requires less fluid pressure than the STS system and can usually be installed in conventional machine tools without major reconstruction.
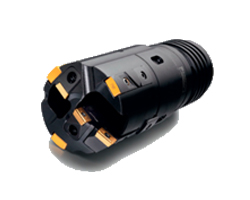
High pressure pumps supply cutting fluid down the outside of the drill tube, between the drill and the drilled hole. The drill shank itself is hollow, and the fluid pressure flushes the chips into the drill body through chip rooms in the drill head, and back out through the drill tube. The high cutting fluid pressure makes the STS-system more reliable than the Ejector system especially when drilling materials where good chip breaking is difficult to obtain i.e. low carbon steels and stainless. The STS-system is always the first choice for long series production.
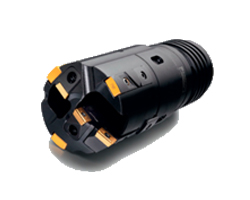
Counter boring a pre-drilled hole is normally used to obtain better surface finish and tolerances when machining forged, cast, pressed or extruded components. If the machine power is insufficient for solid drilling in one operation, the hole can be pre-drilled with a smaller solid drill and then counter bored to the desired diameter. Hardening, tempering, stress relief annealing or other operations are sometimes performed between solid drilling and counter boring.
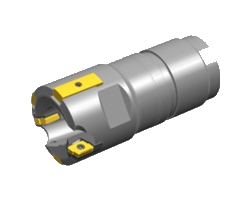
Trepanning is performed without pre-drilling, but instead of machining away all the material in the form of chips, the tool leaves a solid core in the middle of the hole. This method is chiefly used when machine power is limited, since the power requirement is lower than in solid drilling. In the case of large and expensive work pieces, it may be difficult to obtain suitable sample material. The core can then be used for tensile test specimens and material analysis. Particularly in the case of expensive material, the core should be recovered and used for other purposes. Note: In the drilling of blind holes, a special tool is needed to crop off the core. In deep holes, the core will deflect because of it’s own weight and must be supported to prevent problems with insert breakages.
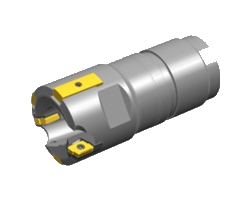