Gun Drilling System
Gun drilling is a process that produces deep, straight holes in a variety of materials. A gundrill tool differs from a conventional twist drill by its unique head geometry a standard gundrill has a single effective cutting edge. Guide pads burnish the hole while drilling, allowing the hole to maintain straightness. The result of this burnishing activity is a very round hole with a precision diameter.
Gun drilling was initially developed for drilling gun barrels. Armament manufacturing continues to be a common use of this process. Other common industries include energy, oil and gas exploration, engines, diesel fuel components, and plastic injection molds. Holes deeper than 20:1 generally require a dedicated gundrilling machine to achieve highest productivity and process reliability.
Gun drilling differs from BTA drilling due to the coolant entry and chip removal. Gundrills introduce coolant through a small hole within the tool, and chip removal occurs through a groove outside the tool. BTA drilling has fluid enter through a mechanism around the tool, while chips are evacuated through the drill itself. BTA drilling becomes more effective than gundrilling around a 50mm hole diameter.
Types of Gun drilling Components
CoroDrill achieves a secure deep hole machining process with indexable insert technology. Up to 15x hole diameter can be drilled in a conventional machine, without moving the work piece to a dedicated deep-hole drilling machine. CoroDrill provides high productivity and reliability achieving a surface finish comparable with traditional deep hole drilling. Single set-up machining of deep holes Achieves same quality as deep-hole drilling Insert geometries and grades for all materials apart from ISO Highly effective chip evacuation No extra coolant-pump capacity required Wide availability of standard tools
A conventional gun drill has a hole in its carbide tip underneath the cutting edge. Pressurized cutting fluid is pumped through the tool’s body and out the hole. The fluid serves a three-fold purpose: it lubricates and cools the cutting edge; it forces the chips back along the flute in the tool body; and it helps to stiffen the shank of the tool. A new design has one hole in the top of the tool tip that effectively directs fluid at the cutting edge. The other hole, which is in the conventional location, helps to provide the chip ejection function. Total flow of cutting fluid is doubled with this two-hole arrangement. More importantly, the design produces chips about half the size of a conventional gun drill of the same diameter using the same speed and feed rate, so that packing of chips along the tool’s shank is avoided in most materials. Recently, coatings such as titanium nitride are being applied to gun drill tips to extend tool life. Physical Vapour Deposition (PVD) is the only practical process for depositing coatings on precision tools such as gun drills, but the results have not been encouraging. Unlike coating high-speed steel tools, PVD coating of a carbide gun drill tip does not seem to form a good metallurgical bond. The coating wipes off during the metal cutting process. Using Chemical Vapour Deposition (CVD) will form a metallurgical bond between the coating and carbide substrate, but the high heat required by the process distorts the tool. Hopefully these problems will be resolved in the near future.
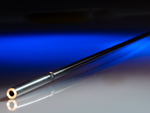
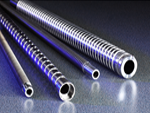
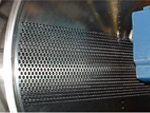
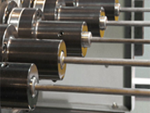